17-4 Stainless Steel Properties: A Comprehensive Examination
Delve into the intricacies of 17-4 stainless steel properties with this comprehensive guide. Explore its unique characteristics, applications, and advantages in various industries.
Introduction
17-4 stainless steel is a high-performance material belonging to the category of precipitation-hardening stainless steels. It's renowned for its exceptional strength and commendable corrosion resistance. This specific type of stainless steel achieves its superior properties through a unique combination of elements in its composition and the ability to be strengthened further via heat treatment.
Composition and Manufacturing Process
Chemical Composition of 17-4 Stainless Steel
17-4 stainless steel derives its name from its key constituents:
- Chromium (17%): Imparts the characteristic corrosion resistance associated with stainless steels.
- Nickel (4%): Enhances strength, toughness, and formability.
- Copper (3-5%): Plays a crucial role in the precipitation hardening process, further improving strength.
- Other elements: Small amounts of manganese, silicon, phosphorus, and niobium are also present, each contributing to specific properties.
Metallurgical Processes Involved in Manufacturing
The manufacturing process of 17-4 stainless steel involves several key stages:
Melting: Raw materials like chromium, nickel, iron, and other elements are melted together in an induction furnace or similar equipment to form a molten alloy.
Casting: The molten metal is poured into molds and allowed to solidify. This initial stage results in a semi-finished product.
Hot Working: The cast ingot undergoes processes like forging or rolling at high temperatures. This refines the grain structure and improves the material's overall mechanical properties.
Solution Annealing: The steel is heated to a specific temperature (around 1038°C or 1900°F) and then rapidly cooled. This creates a uniform microstructure and enhances its formability for subsequent shaping.
Cold Working (Optional): Depending on the desired final shape, the steel may undergo cold working processes like drawing or forming at room temperature. This further strengthens the material but reduces its ductility.
Precipitation Hardening: This is the crucial step that distinguishes 17-4 stainless steel from other types. The solution-annealed material is heated to a lower temperature (around 482°C or 900°F) and held for a specific time. This allows tiny particles of copper compounds to precipitate within the steel matrix, significantly increasing its hardness and strength.
Other Considerations:
The specific processing parameters like temperatures and holding times can be adjusted to achieve different property variations within the 17-4 stainless steel category. These variations are often designated by codes like H925, H1025, etc.
Understanding the interaction between the elements and the heat treatment processes is vital for controlling the final properties of 17-4 stainless steel.
Mechanical Properties of 17-4 Stainless Steel
17-4 stainless steel offers a compelling combination of mechanical properties, making it a valuable material for various applications. Here's a breakdown of its key characteristics:
Property | Description |
---|---|
Strength | Very high tensile strength |
Hardness | High hardness achievable through precipitation hardening |
Ductility | Moderate, allowing for some cold forming |
Toughness | Good, able to absorb impact energy |
Corrosion Resistance | Good, comparable to 304 stainless steel |
Strength and Hardness Characteristics
- High Strength: 17-4 boasts exceptional tensile strength, exceeding most other stainless steels. This makes it suitable for applications requiring components to withstand significant loads.
- Hardness: Through precipitation hardening, 17-4 achieves remarkable hardness, enabling it to resist wear and deformation.
Ductility and Toughness
- Ductility: While not as ductile as some other stainless steels, 17-4 exhibits sufficient ductility to allow for moderate cold forming operations. This allows for some shaping after the solution annealing stage.
- Toughness: 17-4 demonstrates good toughness, implying its ability to absorb energy and resist fracture under impact loads. This makes it suitable for applications where components experience shock or sudden loading.
Corrosion Resistance
Good Corrosion Resistance: 17-4 offers good resistance to corrosion in various environments, comparable to the widely used 304 stainless steel. It performs well in atmospheric conditions, fresh water, and mild chemical solutions.
Other Considerations:
- Strength and hardness of 17-4 can be tailored through variations in the precipitation hardening process. However, this often comes at the expense of ductility.
- For applications requiring exceptional formability and weldability, other stainless steel grades might be better suited.
Heat Treatment in 17-4 Stainless Steel
Heat treatment plays a pivotal role in unlocking the exceptional properties of 17-4 stainless steel. Here's a closer look at the crucial aspects:
Aging Process and its Impact on Properties
The aging process, also known as precipitation hardening, involves a two-step heat treatment:
Solution Annealing: The steel is heated to a high temperature (around 1900°F) and rapidly cooled. This dissolves most of the copper throughout the material, resulting in a soft and workable state.
Aging: The solution-annealed material is then heated to a lower temperature (around 900°F) and held for a specific time (typically 1 hour). This allows the dissolved copper to precipitate out as tiny, dispersed particles within the steel matrix.
This aging process significantly alters the material's properties:
- Increased Strength and Hardness: The formation of these copper precipitates creates internal stresses and acts as barriers to dislocation movement, the primary mechanism by which metals deform. This significantly strengthens the steel and enhances its hardness.
- Reduced Ductility: The presence of the precipitates hinders the metal's ability to deform plastically, leading to a decrease in ductility.
Precipitation Hardening Mechanisms
The strengthening mechanism in 17-4 stainless steel is attributed to two main factors:
Strain Hardening: As the material undergoes plastic deformation during forming processes, dislocations (imperfections in the crystal lattice) get tangled and interact with each other. This makes it increasingly difficult for further dislocation movement, leading to a work-hardening effect and increased strength.
Precipitation Strengthening: The tiny copper precipitates act as obstacles to dislocation movement. When the metal is subjected to stress, dislocations encounter these precipitates, requiring additional energy to bypass them. This significantly impedes plastic deformation and bolsters the material's strength.
Other Considerations:
- The aging temperature and holding time can be precisely controlled to achieve different combinations of strength and ductility. Higher aging temperatures and longer times result in greater precipitation, leading to higher strength but lower ductility.
- Several variations of the aging process exist, designated by codes like H900, H1025, etc. Each code represents a specific combination of temperature and time, leading to tailored properties.
Understanding the interplay between heat treatment parameters and the resulting microstructure is essential for optimizing the properties of 17-4 stainless steel for specific applications.
Applications Across Industries: 17-4 Stainless Steel's Versatility
17-4 stainless steel's unique blend of strength, corrosion resistance, and formability makes it a sought-after material across various industries. Here's a glimpse into its applications in specific sectors:
Aerospace and Aviation
- High-strength components: Due to its exceptional strength-to-weight ratio, 17-4 finds application in aircraft landing gear components, helicopter rotor blades, and structural elements.
- Corrosion resistance in harsh environments: Its ability to withstand challenging conditions makes it suitable for engine cowlings, exhaust manifolds, and parts exposed to de-icing fluids.
Medical Devices and Implants
- Biocompatible: The material exhibits good biocompatibility, making it suitable for certain surgical instruments and implant components.
- Strength and wear resistance: Its high strength and resistance to wear and tear make it ideal for bone screws, pins, and other orthopedic devices.
Oil and Gas Exploration
- Downhole equipment: The ability to withstand high pressure, corrosive environments, and elevated temperatures makes 17-4 suitable for drill bits, well completion components, and valves.
- Strength for demanding applications: Its high strength allows for components that can handle the significant loads encountered during drilling and extraction processes.
Automotive and Transportation
- High-performance components: 17-4 finds use in suspension components, brake calipers, and other parts requiring a combination of strength and weight reduction.
- Corrosion resistance for extended service life: Its resistance to corrosion ensures the durability of these components in challenging weather conditions encountered by vehicles.
Advantages and Limitations of 17-4 Stainless Steel
Advantages of 17-4 stainless steel
- Exceptional Strength and Hardness: Due to precipitation hardening, 17-4 boasts superior strength and hardness compared to many other stainless steels. This makes it ideal for applications requiring high load-bearing capacity and resistance to wear and tear.
- Good Corrosion Resistance: While not the most corrosion-resistant stainless steel type, 17-4 offers good performance in various environments, comparable to 304 stainless steel. This allows it to withstand exposure to weather, fresh water, and mild chemicals.
- Moderate Formability: Although not as easily shaped as some other stainless steels, 17-4 exhibits sufficient ductility to undergo cold working processes like bending and drawing to a certain extent. This enables the creation of moderately complex shapes.
- Weldability using common techniques: 17-4 can be joined using conventional welding procedures like gas tungsten arc welding (GTAW) and shielded metal arc welding (SMAW). This simplifies fabrication processes.
- High-Performance Material for Demanding Applications: The combination of strength, corrosion resistance, formability, and weldability makes 17-4 a valuable material for applications in harsh environments and demanding service conditions.
Limitations and considerations for use
- Lower Ductility Compared to Some Other Stainless Steels: Due to the strengthening mechanisms involved, 17-4 typically has lower ductility than some other stainless steel grades. This means it may not be the best choice for applications requiring extensive forming or bending.
- Strength and Ductility Trade-off: The aging process allows tailoring the strength of 17-4. However, achieving higher strength often comes at the expense of ductility. Careful selection of the aging parameters is crucial to achieve the desired balance between these properties for a specific application.
- Higher Cost Compared to Some Other Stainless Steel Grades: The complex manufacturing process and the addition of elements like nickel and copper contribute to a higher cost compared to some other stainless steels. This needs to be factored into the material selection process.
- May Require Specific Heat Treatment Processes: To achieve the desired combination of strength and ductility, 17-4 often necessitates precisely controlled heat treatment procedures. This adds to the processing complexity and cost.
Overall, 17-4 stainless steel offers a valuable combination of properties, making it suitable for various applications. However, careful consideration of its limitations and potential trade-offs is crucial during material selection. Understanding the specific requirements of the application and comparing 17-4 with other candidate materials is essential to ensure optimal performance and cost-effectiveness.
Comparison with Other Stainless Steels
Contrasting properties with other stainless steel grades
Here's a table comparing key properties of 17-4 stainless steel with commonly used grades:
Property | 17-4 PH | 304 | 316 |
---|---|---|---|
Strength | High | Moderate | Moderate |
Hardness | High | Moderate | Moderate |
Formability | Moderate | High | Good |
Corrosion Resistance | Good | Good | Excellent |
Machinability | Moderate | Excellent | Excellent |
Weldability | Good | Excellent | Excellent |
Cost | High | Moderate | High |
Advantages of 17-4 over alternative materials
While the specific choice depends on the application requirements, 17-4 stainless steel offers some advantages over other common grades:
- Superior Strength: Compared to 304 and 316 stainless steels, 17-4 boasts significantly higher strength and hardness due to precipitation hardening. This makes it ideal for applications demanding exceptional load-bearing capacity and resistance to wear.
- Favorable Strength-to-Weight Ratio: 17-4's high strength combined with its moderate density results in a superior strength-to-weight ratio compared to many other stainless steels. This is crucial in applications where weight reduction is a critical factor, such as aerospace components.
- Good Corrosion Resistance in Specific Environments: While not the most corrosion-resistant overall, 17-4 offers good performance in environments similar to 304 stainless steel. This makes it suitable for various applications like handling fresh water, mild chemicals, and atmospheric conditions.
Additional Considerations
- 304 Stainless Steel: A widely used general-purpose stainless steel known for its excellent formability, weldability, and good corrosion resistance at a moderate cost. It might be a better choice for applications prioritizing these aspects and where high strength is not essential.
- 316 Stainless Steel: Offers superior corrosion resistance compared to 17-4 and 304, making it suitable for harsher environments like marine applications or chemical processing involving strong acids. However, its strength is similar to 304 and lower than 17-4.
In conclusion, 17-4 stainless steel stands out for its exceptional strength and good balance of other properties. When an application demands a high strength-to-weight ratio, good corrosion resistance, and reasonable formability, 17-4 can be a preferable choice compared to other commonly used stainless steel grades.
Future Trends and Developments in 17-4 Stainless Steel
The unique properties of 17-4 stainless steel position it for continued relevance and potential advancements in various sectors. Here's a glimpse into what the future might hold:
Emerging Applications
- Additive Manufacturing: Advancements in 3D printing technologies using metal powders could open doors for the creation of complex 17-4 components with tailored properties. This would enable innovative designs and lightweight structures in industries like aerospace and automotive.
- Biomedical Engineering: Research into improving the biocompatibility of 17-4 could lead to its wider adoption in medical implants requiring high strength and wear resistance, potentially for applications like joint replacements and trauma fixation devices.
- Extreme Environment Applications: The ongoing development of variants with enhanced corrosion resistance could expand the use of 17-4 in demanding environments like offshore oil and gas exploration or components exposed to harsh chemicals.
Research and Advancements in 17-4 Stainless Steel
- Microalloying and Processing Techniques: Research into incorporating minor elements or utilizing specific processing methods might lead to 17-4 variations with improved properties like even higher strength, enhanced corrosion resistance, or better formability.
- Novel Heat Treatment Processes: Developing new and optimized heat treatment procedures could allow for finer control over the microstructure and achieving a wider range of property combinations within the 17-4 stainless steel category.
- Sustainability Considerations: Research efforts might focus on developing more sustainable manufacturing processes for 17-4, potentially involving the use of recycled materials or reducing the environmental impact of processing steps.
Additional Thoughts
- The increasing demand for lightweight, high-performance materials in various industries is likely to continue driving innovation in 17-4 stainless steel.
- Advancements in computational modeling and simulation tools could aid in designing and optimizing 17-4 components for specific applications.
- Continued research into understanding the interaction between microstructure, properties, and performance of 17-4 will be crucial for unlocking its full potential in future applications.
In conclusion, 17-4 stainless steel holds promise for continued advancements and exploration of new applications. With ongoing research and development efforts, this versatile material can play an even more significant role in various industries in the years to come.
Conclusion
17-4 stainless steel is a high-performance material renowned for its exceptional strength and good corrosion resistance. This unique combination is achieved through its specific composition and the ability to be further strengthened via precipitation hardening.
With its potential for further advancements, 17-4 stainless steel is poised to play an even more significant role in diverse industries in the future.
Discover Strength and Durability with Unionfab
With decades of experience supplying the automotive, medical and consumer industries, we understand the importance of reliability. From prototyping through full-scale production, customers trust us to provide materials unequaled in strength, corrosion resistance and other physical properties.
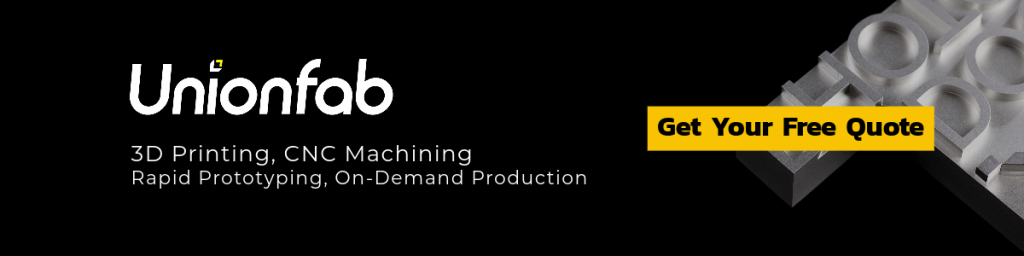